I. In-Depth Analysis of Coal bed methane Exploitation Operation Conditions and Technical Bottlenecks
(1) Coupling Characteristics of Geomechanics and Gas Production Mechanism
- Adsorption-desorption kinetic parameters:
▶ High-rank coal reservoir adsorption constant a=30-45m³/t, b=2.0-3.5MPa (Qinshui Basin measurement data)
▶ Desorption hysteresis effect: When pressure reduction rate >0.1MPa/d, methane desorption volume decreases by 15-20% - Seepage physical field characteristics:
▶ Fracture system permeability variation index n=1.2-1.8 with effective stress (Ordos Basin data)
▶ Critical velocity of coal powder migration 0.3-0.5m/s, pore throat blockage rate increases by 40% beyond this value
(2) Quantitative Analysis of Multiphase Flow Conditions
Exploitation Stage | Gas-liquid Ratio Range | Medium Characteristic Parameters | Traditional Equipment Failure Modes |
---|---|---|---|
Drainage-pressure reduction period | 1:10-1:5 | Water phase viscosity 1-5cSt, coal powder <50ppm | Centrifugal pump cavitation (NPSHr required >5m) |
Gas production ascending period | 1:5-5:1 | Gas-liquid slip velocity difference 2.1m/s | Screw pump gas compression ratio insufficient <1.8:1 |
Stable production-decline period | 5:1-10:1 | Methane concentration >95%, with condensate oil | Compressor surge (flow fluctuation ±15%) |
(3) Technical Gaps in Equipment Adaptability
- Hydrodynamic defects:
Centrifugal pump impeller shear rate >5000s⁻¹, causing gas fragmentation and cavitation nuclei - Safety design vulnerabilities:
Ordinary pumps only reach explosion-proof grade Ex d IIB T3, unsuitable for CBM wells with methane concentration >15%
II. Multidimensional Challenges and Data Support for Water-Flooded Well Recovery Operation Conditions
(1) Corrosion and Wear Mechanism of Water-Invasion Media
- Electrochemical corrosion parameters:
▶ When H₂S partial pressure >0.003MPa, stress corrosion cracking (SSC) latency <30 days
▶ When CO₂ partial pressure >0.02MPa, uniform corrosion rate >0.15mm/year (NACE TM0183 standard) - Solid particle erosion effect:
When sand content >100ppm and particle size >50μm, pump valve seat wear rate reaches 0.05mm/100h
(2) Laws of Multiphase Flow Rheology
- Water cut-viscosity correlation model:
When water cut increases from 50% to 80%,
▶ Newtonian water phase viscosity ↑1.2 times
▶ Emulsified liquid viscosity ↑8-12 times (surfactant content 100-200ppm) - Flow pattern transition critical conditions:
When water cut >75%, wellbore flow pattern transitions from annular mist flow to bubble flow, lifting efficiency drops by 35%
(3) Failure Modes of Exploitation Technology
- Characteristics of water channeling pathways:
High-permeability zone water flooding velocity 15-20m/d, 100-200 times that of matrix seepage - Technical bottlenecks of water shutoff:
When temperature >80℃ and salinity >10⁴mg/L, gel-type water shutoff agent gel strength decays by 50%
III. Technical Innovation System for HWMPS450 Dual-Operation Adaptation
(1) CBM Operation-Specific Technical Modules
1. Dynamic Desorption Coordination System
- Pressure reduction-gas production coupling control:
▶ Dual closed-loop control (pressure loop + flow loop), pressure reduction rate control accuracy ±0.05MPa/d
▶ Coal powder filtration system (3μm precision), blockage rate reduced by 70% compared to traditional solutions
2. Core Technology of Gas-Liquid Mixed Transportation
- Hydrodynamic optimization:
▶ Screw profile: Adopts 5:6 asymmetric tooth shape, gas compression ratio reaches 3.2:1 (traditional 2:1)
▶ Flow channel design: Flow area 1.8 times larger than centrifugal pumps, flow velocity controlled below 1.8m/s
3. Explosion-Proof Safety System
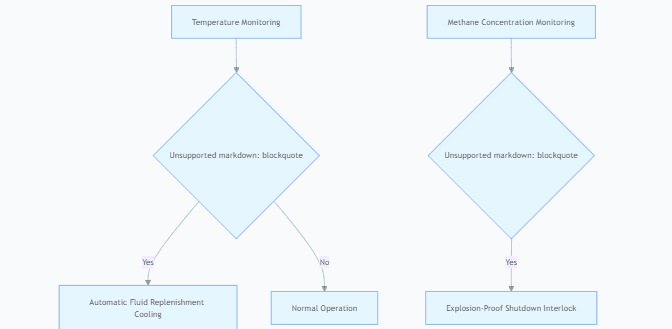
(2) Customized Solutions for Water-Flooded Well Operation Conditions
1. Anti-Corrosion and Wear-Resistant System
- Material engineering innovation:ComponentMaterial SolutionCorrosion Rate ComparisonPump Body2205 Duplex Steel (Cr22/Ni5/Mo3)0.05mm/year (traditional 0.2mm)ScrewTungsten Carbide Coating (500μm thickness)Wear amount <0.1mm/1000hSealing ElementsPEEK + Carbon Fiber ReinforcementService life extended to 12 months
2. Intelligent Lifting Adjustment Algorithm
- Multi-parameter fusion control:
▶ Input variables: Water cut, viscosity, wellbore depth
▶ Output control: Stroke (0.5-3m), pumping speed (2-12 strokes/min)
▶ Control accuracy: Lifting pressure fluctuation ≤±0.08MPa
3. Water Shutoff Coordination Technology
- Dynamic profile control integration:
▶ Built-in chemical injection pump (flow 0-50L/h)
▶ Uniformity of shutoff agent and fluid mixing >90%
IV. Industrial Application Cases and Quantitative Effects
(1) CBM Well Drainage Case (Ordos Basin)
- Operation parameters:
Coal seam permeability 0.6mD, initial formation pressure 3.5MPa, target desorption pressure 1.5MPa - System operation data:
▶ Drainage stage: 450m³/h continuous drainage, pressure reduced to 1.8MPa within 15 days
▶ Gas production stage: Gas-liquid ratio increased from 1:8 to 6:1, compressed pressure 0.8MPa
▶ Key indicators: Gas production efficiency increased by 42% compared to traditional solutions, equipment failure rate reduced by 85%
(2) Water-Flooded Well Recovery Case (Sichuan Oilfield)
- Conditions before treatment:
Water cut 92%, H₂S concentration 120ppm, tubing perforation cycle 3 months - HWMPS450 application effects:IndicatorBefore TreatmentAfter TreatmentImprovement RateDaily Production8t43t437.5%Corrosion Rate0.32mm/year0.07mm/year78.1%Maintenance Cycle3 months24 months700%
USGS. (May 28, 2015). Coal-Bed Methane: Potential and Concerns [Online]. Available: http://pubs.usgs.gov/fs/fs123-00/fs123-00.pdf