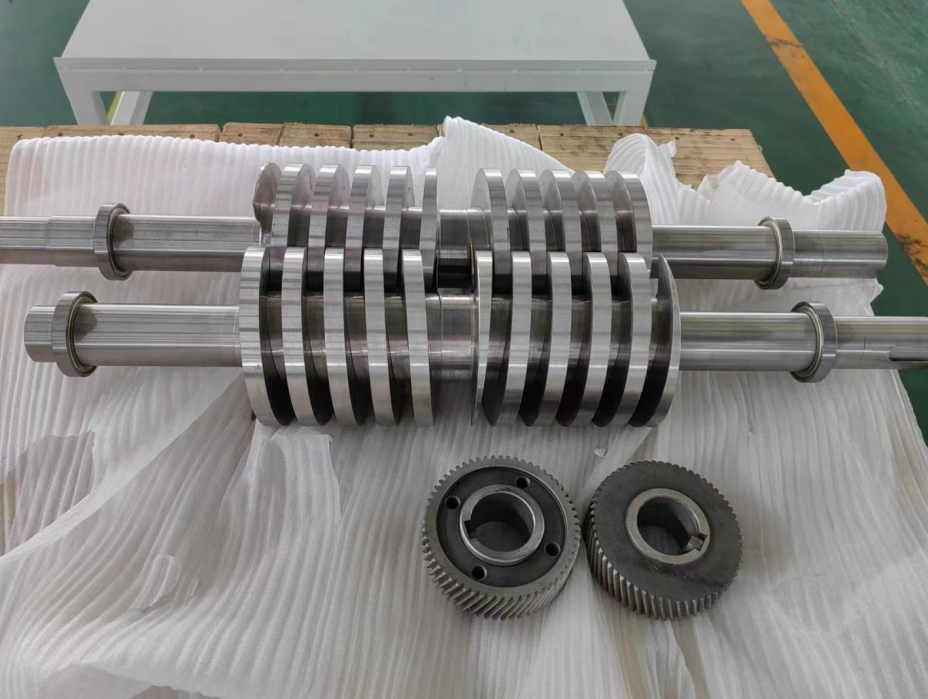
As professional screw pump manufacturers, we are well – aware of the significance of each part of the screw pump for the efficient and stable operation of the equipment. During long – term use, the parts of the screw pump are inevitably affected by factors such as wear and aging, which may impact their performance. Therefore, with our profound professional technology and rich experience, we provide a full range of screw pump parts manufacturing services to meet the needs of maintenance and replacement for our customers. Next, we will introduce the key parts of the screw pump in detail.
1.Screws – The Core Driving Force for Transportation
The screws can be regarded as the heart of the screw pump. Generally, they consist of a driving screw and one or more driven screws. The driving screw is driven to rotate by an external power source, which in turn drives the driven screws to rotate synchronously. The unique spiral shape and pitch design of the screws directly determine the flow rate, pressure, and transportation efficiency of the pump. During operation, the screws mesh closely with each other to form continuous sealed chambers, smoothly pushing the fluid axially from the suction end to the discharge end.
As professional manufacturers, we use high – quality alloy steel materials to manufacture screws. Starting from forging, it goes through multiple processes such as precision turning and grinding. The selected materials have high strength, excellent wear resistance, and good corrosion resistance, ensuring that the screws can operate stably for a long time in various media and working conditions. At the same time, we use advanced CNC machining equipment and precision testing instruments to strictly control the dimensional accuracy and surface finish of the screws, so that the clearance between the screws and the inside of the pump body reaches the optimal state, reducing leakage and improving the volumetric efficiency of the pump.
2.Pump Body – The Solid and Stable Guardian
The pump body, as the sturdy outer shell of the screw pump, not only provides support and containment for the internal parts but also serves as a key passage for fluid transportation. It is usually made of high – strength cast iron or cast steel and is formed through a precision casting process to ensure structural strength and dimensional accuracy. The inside of the pump body is machined with spiral chambers that match the screws, and its shape and size have a significant impact on the performance of the screw pump.
As professional screw pump manufacturers, we deeply integrate the principles of fluid dynamics in the design of the pump body, carefully optimize the contour of the spiral chamber to reduce fluid transportation resistance and energy loss. According to different working pressure and temperature requirements, we reasonably design the wall thickness of the pump body and use non – destructive testing and other methods to ensure that there are no internal defects in the pump body, guaranteeing its safety and reliability under harsh working conditions such as high pressure and high temperature.
3.Bushings – The Pillars of Sealing and Support
The bushings are installed between the pump body and the screws, taking on the dual responsibilities of sealing and supporting the screws. They effectively prevent fluid leakage and at the same time bear the radial and axial forces generated by the rotation of the screws, reducing the wear between the screws and the pump body. Bushings are generally made of wear – resistant and corrosion – resistant materials, such as bronze and special engineering plastics.
The bushings we provide are accurately selected with the most suitable materials according to different application scenarios and medium characteristics, and advanced manufacturing processes are used to ensure the dimensional accuracy and surface quality of the bushings. The inner surface of the bushing is specially treated to have an extremely low friction coefficient, effectively reducing the wear between the screw and the bushing and extending the service life of both. At the same time, we strictly control the fitting accuracy between the bushing, the pump body, and the screw to ensure reliable sealing performance.
4.Shaft Sealing Devices – The Loyal Guards Against Leakage
The function of the shaft sealing device is to prevent the fluid in the pump from leaking out along the shaft of the driving screw and to prevent outside air from entering the pump. The common shaft sealing forms include mechanical seals and packing seals. Mechanical seals have good sealing performance, low leakage, and a long service life, and are often used in occasions with strict leakage requirements; packing seals have a simple structure and low cost and are suitable for working conditions with relatively low sealing requirements.
As professional screw pump manufacturers, we can provide various shaft sealing devices according to the actual needs of users. For mechanical seals, we select high – quality sealing materials such as silicon carbide and cemented carbide to ensure good sealing performance under harsh conditions such as high speed, high pressure, and high temperature. We manufacture and assemble them strictly according to the design requirements to ensure the flatness and perpendicularity of the sealing surface and extend the service life of the mechanical seal. For packing seals, we select high – performance packing materials and optimize the installation process to ensure the reliability and maintainability of the packing seal.
5.Bearings – The Reliable Guarantee for Smooth Operation
Bearings are used to support the rotation of the screws, bear the radial and axial forces generated during the operation of the screws, and ensure the smooth rotation of the screws. According to the structure and working requirements of the screw pump, the commonly used bearings are rolling bearings and sliding bearings. Rolling bearings have a small friction coefficient, low starting resistance, and high efficiency; sliding bearings have a large load – bearing capacity, smooth operation, and low noise.
As professional manufacturers, when selecting bearings, we fully consider the working conditions and load of the screw pump and select the appropriate type and specification of bearings. For screw pumps with high – speed and light – load operation, we usually use high – precision rolling bearings and ensure their efficient operation through reasonable installation and lubrication design. For screw pumps with low – speed and heavy – load operation, we select sliding bearings with a strong load – bearing capacity and improve their wear – resistant performance and service life by optimizing the bearing structure and materials.
Regardless of what parts your screw pump needs for repair or replacement, as professional screw pump manufacturers, we can, with our professional technology and rich experience, provide you with high – quality products and services to ensure that your screw pump quickly returns to its best operating state.